Advanced Welding WPS: Customizing Specifications for Complicated Projects
Advanced Welding WPS: Customizing Specifications for Complicated Projects
Blog Article
Understanding Welding WPS Standards: Best Practices and Techniques for Quality Welds
In the world of welding, grasping Welding Treatment Requirements (WPS) criteria is an essential element that directly influences the quality and stability of welds. Abiding by these requirements makes sure uniformity and dependability in welding outcomes. However, achieving excellence in welds goes beyond just understanding the requirements; it entails applying best methods and methods that elevate the craft to a level of accuracy and ability that distinguishes the standard from the remarkable. As we browse with the ins and outs of welding WPS standards, discovering essential understandings and strategies for attaining top-tier welds will be critical for welders looking for to master their craft and generate welds that stand the test of time.
Recognizing Welding WPS Standards
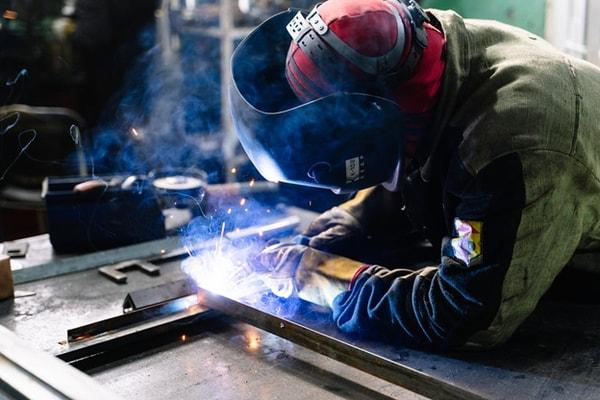
Understanding WPS standards is crucial for welders, engineers, and inspectors included in welding operations. By complying with WPS guidelines, welders can produce welds that fulfill the needed mechanical buildings and structural integrity. Inspectors rely on WPS paperwork to confirm that welding procedures are being adhered to properly and that the resulting welds are of top quality. Designers utilize WPS standards to create welding procedures that guarantee the sturdiness and dependability of bonded structures.
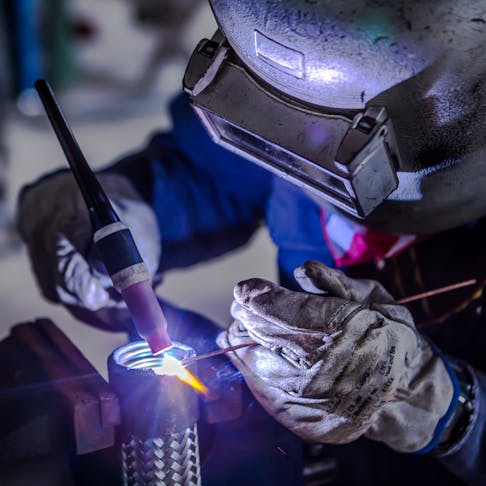

Essential Devices for Quality Welds
Grasping welding WPS requirements is necessary for welders to properly use the important devices required for creating top quality welds. The kind of welding equipment needed depends on the welding process being utilized, such as MIG, TIG, or stick welding. Wire brushes and cracking hammers are vital for cleansing the weld joint before and after welding to get rid of any kind of pollutants that could influence the high quality of the weld.
Key Techniques for Welding Success
To accomplish welding success, one need to understand the crucial techniques important for creating premium welds. One vital method is maintaining the appropriate arc length. Maintaining the electrode at the ideal distance from the workpiece is crucial for creating strong, consistent welds. In addition, regulating the travel rate is vital. Relocating too promptly can lead to insufficient infiltration, while moving as well slowly can result in too much warmth input and potential issues. Proper control of the electrode angle is an additional important technique. The angle at which the electrode is held can impact the bead shape and infiltration of the weld. Additionally, guaranteeing constant weapon angle and instructions of traveling is important for harmony in the weld grain. Finally, preserving a secure welding and a constant hand setting throughout the process is essential to attaining precision and uniformity in the welds. By grasping these essential methods, welders can raise the quality of their work and attain welding success.
Ensuring Compliance With WPS Specifications
In addition, keeping in-depth records of welding criteria, equipment calibration, and inspection outcomes is crucial for showing compliance with WPS standards. By carefully adhering to WPS standards, welders can make certain that their job satisfies the needed quality degrees and adds to the overall success of the welding task.
Troubleshooting Common Welding Issues
When confronted with typical welding problems, identifying the origin is essential for efficient troubleshooting. One common trouble is the visibility of porosity in welds, often created by pollutants such as rust, oil, or wetness. To resolve this, guaranteeing correct cleaning of the base steel before welding and utilizing the correct protecting gas can substantially decrease porosity. Another concern regularly official site run into is lack of fusion, where the weld fails to effectively bond with the base material. This can originate from poor warm input or improper welding method. Adjusting parameters such as voltage, wire feed speed, or take a trip speed can aid improve fusion. In addition, distortion, cracking, and spatter prevail welding challenges that can be reduced with correct joint prep work, constant warmth control, and picking the appropriate welding consumables. By completely recognizing these common welding problems and their source, welders can successfully troubleshoot issues and achieve top quality welds.
Final Thought
Finally, grasping welding WPS standards needs a thorough understanding of the standards, making use of essential tools, and carrying out crucial strategies for effective welds. Guaranteeing conformity with WPS criteria is essential for creating top quality welds see page and preventing usual welding issues. By following ideal techniques and methods, welders can accomplish constant and dependable lead to their welding projects.
In the world of welding, understanding Welding Procedure Specification (WPS) standards is a crucial element that straight influences the high quality and integrity of welds.When diving into the world of welding techniques, a critical facet to comprehend is the value and intricacies of Welding Treatment Specification (WPS) requirements. WPS requirements give an in-depth standard for welding procedures, making sure consistency, top quality, and safety and security in the welding process. The kind of welding device required depends on the welding process being utilized, such as MIG, TIG, or stick welding.Achieving welding success via the mastery of vital techniques requires a thorough understanding and adherence to Welding Treatment Specification (WPS) criteria.
Report this page